Domray Oil Filtration
The Domray Oil Electric Filtration units are designed for the tough conditions found in the kitchen and used in many operations across Australia. Available in 40 litre capacity as standard, special sized units can be built to order.
Manufactured in stainless steel construction with a powerful 1/2 hp heavy duty low maintenance pump system and being able to return filtered oil back to the fryer at over 20 litres per minute, the cleaning of fryers and the filtering of oil becomes quick, safe and easy. The return flow to the fryer allows the area around the cold zone to be fully flushed to remove all loose matter at the bottom of the fryer pan. Crumbing in the oil is removed in long lasting washable and reusable filter bags complying with Worldwide food standards.
The Domray Oil Filtration Units have a simple fold down handle and large wheels for easy storage where space is at a premium.
Whilst maintenance is minimal, with all electrics contained in the motor housing and easy access to the pump, no special tools or expertise is needed if required.
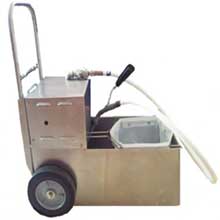
DOM Standard 40 litre
Length: 630mmWidth: 300mm
Height: front: 275mm - rear: 500mm
Handle Extended: 750mm
Operation of the DOM40 Filtration Machine
- Domray Filtration units are made in Australia from a combination of local Australian fabrication and imported Miroil (US) parts which have been used for over 30 years and have a proven record.
- The Domray Filtration Units allow oil falls by gravity through the filter bag so that the loading on the ½ HP motor in the integral pump system is minimal and provides for years of trouble free service.
- With the handle folding down and having large wheels storage in tight kitchen conditions is made easy.
- When filtering it is recommended that the oil temperature should be approx 120C to avoid burns from spilt oil.
- Care should be taken to ensure that all oil discharged from the fryer passes into the filter bag so that all crumbs and matter is collected at this point.
- If matter is allowed to go into the basin then this will be sucked up the inlet of the pump and will enter the pump chamber with possibility of damage to the rollers or cause the impellor to break.
- The unit come complete with its own RB3 filter bag, which has a normal life of between 9-12 months.
- This filter bag will remove all the main solid crumbs from your oil and there is no need for any additional paper filters.
- The crumbs etc collected by the filter bag should be emptied immediately after filtration into the trash unit and the bag should be washed under the hot water tap.
- It is not necessary to remove the bag from the frame when carrying out this washing process. Continual removal of the bag can weaken the bag fasteners reducing the life of the filter bag.
- DETERGENT should never be used when cleaning the bag or the filtration machine.
- Cleaning of the filtration unit only requires hot water and wiping with paper towels or similar.
- DO NOT run hot water through the pump as this will remove essential grease in the pump head and cause the pump to become inoperative.
- Should hot water be applied in error then it may be necessary for oil to be poured down the delivery hose to recharge the pump head.
Troubleshooting
Whilst the level of problems with the pumping system will be minimal due to the fact that the units operates under no load, from time to time clients may experience problems in the operation of the system.
Whilst in most cases any problem will be minimal it could prevent the unit operating. Most problems will be the result of the manner in which the unit has been operated, and can be attributed to procedures, particularly when solid fat is being used, or allowing particles to enter the pump due to oil flow from the fryer not being directed through the filter bag, or washing the pump out with hot water.
Some suggestion on avoiding or fixing these problems in the field are detailed below.
Where solid fat which has been allowed to harden, probably resulting from storage overnight then a plug can be created either in the suction pipe in the basin or in the delivery hose if it has not been hung after use for drainage and avoiding kinks.
When particles are allowed to enter the pump head either as a result of a split bag or oil flow not passing through the filter bag, then an accumulation of particles, particularly with solid fat, will solidify in the pump itself stopping the pump from rotating.
These potential situations can be avoided with correct operation but if you do experience a problem of this nature then the following is a guide to the action which should be taken to bring the machine back into use.
- Ensure basin is empty
- Remove delivery hose and confirm, using hot water that it is clear and there is no plug in the hose.
- Switch on pump and confirm it:
- Runs continuously
- Note any unusual noise in the pumping area
- If the motor and pump appear to be working normally, disconnect the power cord and remove the elbow and connector as one piece from the top of the machine.
- Remove the cover by undoing the two screws at the rear. This will expose the pump and motor.
- Reconnect the power cord and run the motor again, listening for any noise, particularly in the pump area which could be particles in the head.
- At this stage the pump will be exposed. Disconnect the power cord and using an Allen key remove the cover on the pump, noting the position of the raised locator. There are 4 screws attaching the cover.
- Take care as under the cover are 5 round rollers and an impellor.
- Under this conditions it is possible to see if any foreign matter has become lodged in the pump head and also visually inspect the impellor.
- After removing the impellor and rollers, reconnect the power cord and run the motor again to confirm the shaft is turning and the motor operates free from any noise.
- If all appears to be in order, then it is almost certain that the problem is in the suction pipe going to the bottom of the basin from the pump.
- When the cover is removed the top of the suction pipe is exposed and it is possible to pass a wire down from the top and check for a blockage. Solid fat may have congealed in the pipe and this is preventing suction. If so this fat will need to be removed before the pump can run.
- When this action has been completed, reinstall the impellor and fit the rollers and cover of the pump as per the drawing included in this web page under Reassembly of Pump, making sure that the cover is aligned correctly matching the location points.
- Refit the elbow and connector in the top of the pump and attach the delivery hose.
- Fill the basin with a small amount of hot water and make sure the hose is pointed into the basin. It could be best to have someone assist in holding the hose.
- Turn on the pump for a minute and watch to see if water is sucked up and discharged into the basin. DO NOT RUN FOR LONG PERIOD USING HOT WATER
- If the pump operates normally then stop the motor, disconnect the power cord, delivery hose and remove the elbow and connector. Pour some frying oil into the top of the pump housing before reassembling the cover.
- Refit the elbow using plumbing tape to seal.
- When completed connect the discharge hose and pour some more frying oil down the hose into the pump to prime the pump. THE PUMP WILL NOT WORK WITHOUT OIL BEING AVAILABLE IN THE HEAD.
The DOM 40 Filtration Units will give years of valuable trouble free performance given attention to the operating instructions.
Click HERE to download this Troubleshooting Guide in .PDF format (requires Adobe Acrobat Reader).
Warranty Information
The following warrant policy applies to all DOM Filtration Machines.
Loss or damage during shipment
All cartons should be inspected before unpacking. Your Domray units would have been thoroughly inspected prior to dispatch and the carton should be opened on receipt and any damages noted on the carriers delivery note. Notification of any loss or damage must be made to us with 24 hours of receipt.
The units are tested before shipment, and some residual oil may stain the external carton. This should not be evidence of damage.
Warranty
This product is guaranteed against defects in workmanship and materials for one year.
This will not apply to:
- Misuse or negligence or accident.
- Any repairs or alterations outside our factory or authorised service agent.
- Does not include replacement of parts that become inoperative due to normal wear.
- We disclaim all liability for any accident resulting from the misuse of this equipment.
- No warranty, express or implied, may be authorised by any other party on our behalf
- This warranty shall only apply to the original purchaser
Servicing
The motor and integral R40 pump has the on/off switch and male plug socket for connecting the incoming supply fitted into the motor box. The motor is rated at 240 volt 50 cycle supply and has a red overload thermal button.
In the event that an overload occurs, allow several minutes and press to restart. If the unit does not operate, call an electrician to ascertain the cause. The motor can be easily accessed by removing the top elbow connection and two screws in the rear of the casing. When this is done the motor and pump unit is fully displayed. The inlet connection from the basin which screws into the inlet of the pump comprises a castellated base. This controls the amount of residual oil that remains in the basin after filtration.
When using liquid oil this inlet pipe is screwed down low to the basin base and by tilting back the unit very little oil will be left in the basin. If you are using fat which becomes solid on cooling, to avoid plugging in the tube it should be wound up to approx 8-10mm from the base.
To increase the distance from the bottom of the filter:
- Unscrew the two bolts at the rear of the motor cover holding the cover in place.
- Remove the cover to gain access to the back nut on the suction tube.
- Screw the back nut down approx one thread.
- Turn the suction tube anti clockwise to raise the tube.
- Tighten back nut.
- Refit the motor cover.
The delivery hose has been tested for use with hot oil and is the appropriate food grade virgin silicone according to UL #1889 and NSF specifications.
The RB3 Filter bag is made from material complying with Chapter 21 Part 177.1630 of the US Code for Food Safe and Food compatible materials.
For Instructions on Shaft Seal Replacement - Click on image below
DOM 40 Spare Parts
An expanded view of the pump assembly construction including components can be viewed HERE.
Please Note: Adobe Acrobat reader must be installed in order to view this file. This reader can be downloaded from HERE.
Part | Description |
---|---|
Filter Bag |
RB3 - life: approx 500 filtrations |
Filter Frame | DOM2A |
Delivery Hose |
Hose sub assembly: We recommend the replacement periodically of the Hose Sub Assembly, This involves the unscrewing of the ends of the hose and replacing the centre coated hose portion. |
Rollers (5) | Essential to pump speed. 11mm when new and should be looked at after approx 5 years. |
Impellor for R40 |
Only normally requires replacement if something solid is allowed to enter the pump which may cause breakage. |
Supply Lead |
Standard computer lead. 1.2m long. |
ON/OFF Switch | Part 129-426 RS Components |
Male Socket |
Part 488-191 RS Components |
Hose Connector 'O' Ring |
Replace as required to avoid leakage. |